Enzymatic Recycling: Will it Revolutionize Plastic Waste Management?
2024226
James Kennedy
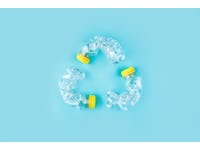
In the face of escalating global plastic pollution, enzymatic recycling has emerged as an innovative approach, capturing media attention by offering a novel solution to one of the most pressing environmental issues of our time. This approach utilizes enzymes, which are biological catalysts, to break down plastics into their constituent monomers, which can then be repurposed to create new plastics. This process not only holds the potential to address the challenges of difficult-to-recycle plastic waste but also to close the loop in plastic manufacturing, contributing to the development of the goal of a truly circular economy. Several emerging players, such as Carbios and Samsara Eco among others, are aiming to be the first to achieve full commercial-scale production.
The Mechanics of Enzymatic Recycling
At the heart of enzymatic recycling is the use of specific enzymes that can target and break down polymers into monomers. Unlike mechanical recycling, which often results in the degradation of plastic quality, enzymatic recycling maintains the integrity of the monomers, allowing them to be reused in high-quality applications.
The process begins with identifying and engineering enzymes capable of degrading various types of plastics. Scientists have discovered and optimized enzymes from different sources, including bacteria and fungi, that can break down polyethylene terephthalate (PET), one of the most common plastics used in bottles and packaging, and other polymers like polyurethane (PU). A notable PETase enzyme (capable of breaking down PET plastic) was discovered in 2016 from Ideonella sakaiensis strain 201-F6 bacteria found in sludge samples collected from a Japanese PET bottle recycling site. Other PET-degrading enzymes were known to exist previously, but this discovery sparked significant interest in the potential for enzymatic recycling. In April 2020, Carbios made headlines with their newly designed hydrolase enzyme, which was able to recycle 90% of PET plastic within a sample within 10 hours.
Advantages Over Traditional Recycling Methods
Enzymatic recycling offers several distinct advantages over traditional mechanical and chemical recycling methods. First, it allows for the recycling of plastics that are difficult to recycle through conventional mechanical means, thus expanding the range of recyclable materials. This includes films and multilayer plastics, which are unable to be recycled with current mechanical methods because these enzymes are not generally affected by the presence of metals or paper components (although enzyme poisoning is a factor to consider). Moreover, it operates under relatively mild conditions—normal temperatures and pressures—making it less energy-intensive and more environmentally friendly than chemical recycling processes that require high temperatures and potentially hazardous chemicals.
Another significant advantage is the quality of the recycled material. Enzymatic recycling can produce monomers that are indistinguishable from those derived from virgin materials, enabling the creation of plastics with no compromise on material properties which is not provided with mechanical recycling. This feature is particularly important in industries where the quality of materials is paramount, such as in medical devices and food packaging. Exact yields from these processes are yet unknown, but the yield from waste plastic to new plastic is likely to be greater than that offered by pyrolysis (one of the leading advanced recycling technologies being touted), and more similar to other chemical depolymerization techniques.
Challenges and Future Directions
Despite its promising capabilities, enzymatic recycling faces several challenges that must be addressed to realize its full potential. One of the main obstacles is the rate of enzyme activity (the rate at which an enzyme catalyzes a specific reaction), which is often too slow for industrial-scale applications. Accelerating the degradation process through enzyme engineering and optimization is a critical area of research.
Another challenge is the economic viability of enzymatic recycling. Developing cost-effective processes for enzyme production and recycling operations is essential to compete with traditional recycling methods and the production of virgin plastics. Additionally, improving the efficiency of the process, including the separation and purification of the resulting monomers, is crucial for reducing costs.
The future of enzymatic recycling depends on continued innovation and research. Advances in biotechnology and genetic engineering hold promise for the discovery and development of more efficient enzymes. Furthermore, integrating enzymatic recycling into existing waste management systems and creating value chains for the recycled monomers will be essential for its adoption on a global scale.
The extent to which emerging research methods, such as machine learning techniques and directed evolution, will reveal new enzymes that are more efficient and able to handle new plastics is unknown, but the scope for improvement has huge potential.
Enzymatic recycling is at the forefront of sustainable solutions to the global plastic waste crisis alongside other advanced recycling approaches such as pyrolysis, gasification, solvent extraction, and chemical depolymerization.
By harnessing the power of enzymes to recycle plastics into high-quality materials, this enzymatic approach has the potential to transform the landscape of plastic manufacturing and waste management. Overcoming the technical and economic challenges will require continued research into improved enzymes, optimization of industrial methods, and investment from both governments and private finance.
However, the potential benefits—a reduction in crude oil-derived virgin plastics plastic, conservation of resources, and promotion of the circular economy—mean that enzymatic recycling is an emerging technology that cannot be ignored.
To explore the full portfolio of sustainability research available from IDTechEx, please visit www.IDTechEx.com/Research/Sustainability.